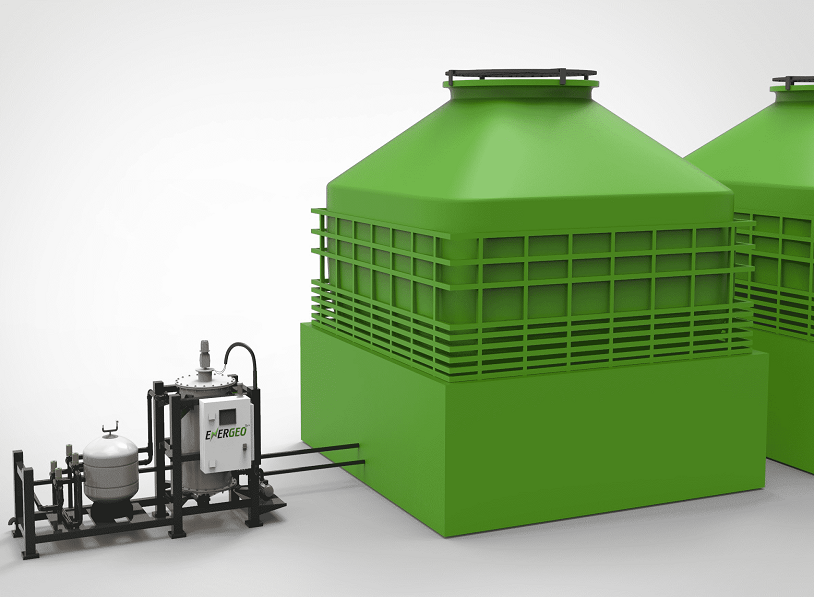
Water evaporation is used in cooling towers to remove surplus heat and cool the working
fluid. Cooling towers use air-cooling or similar dry rejection technology to keep water
temperatures low. It is not only cost effective, but also an energy efficient cooling system.
Cooling towers are classified into three types: counter flow, cross flow, and hyperbolic.
A chiller is often an equipment that aids in the removal of heat from a liquid by absorption or
vapour compression. Normally, the liquid flows through the heat to cool the specific
equipment. The range and approach of chillers and cooling towers are used to rate them.
This is also dependent on the sort of temperature. Many dangerous substances are utilized in
chillers and cooling towers.
Acid is used in cooling towers, which can cause oxidation or scaling. Sulfate ions (SO4-2) are
introduced into regular water by sulfuric acid. Depending on the temperature, this may
eventually result in calcium sulfate deposition.
To avoid the usage of chemicals, it is critical to employ non-chemical treatment for chillers
and cooling towers. This may be accomplished through the application of advanced system
technologies.
A progressive method can aid in the elimination of numerous chemical-related issues.
Because of the negative side effects, many cooling plants avoid using chemicals. The
advanced technology tries to develop a solution that will accomplish the objective while
causing no harm to the plant.
All Of The Following Issues Can Be Solved Using Technology
1. The scaling problem — As the water evaporates from the cooling tower, the
concentration of the solid grows significantly. Furthermore, if the concentration
exceeds the temperature, scaling occurs. The solids in the system can scale.
The Progressive method may eliminate scaling without the need of any chemicals.
2. Fouling — It is the accumulation of tiny deposits on the heat surfaces of cooling
towers. Heat exchange performance can be hindered by fouling. Different forms of
fouling are caused by chemical changes within the liquid base. Deposits on the tube
surface are also caused by fouling.
Cleaning the system does not have to be done using chemicals. This will truly aid in
improving performance. To begin, existing cooling towers must be cleaned before a
progressive system can take over. With this procedure, there will be no particles in the
cooling system.
3. Corrosion — Corrosion usually prevents metal loss, which leads to crucial system
failure in cooling towers. It controls the water pipelines as well as the cooling
equipment. Corrosion usually happens when metals try to revert to their native
condition.
Corrosion may be avoided by employing a cutting-edge technological system. The
system is designed to work in a saturated environment that is inherently non-
corrosive. There is no additional danger of chemical corrosion with this approach. It is
a safe method of preventing the issue in cooling towers.
The Dangers of Chemical Use in Cooling Towers
1. Problem with high blowdown — Cooling towers evaporate water. Large particles
remain after evaporation, resulting in a blowdown. When the cooling plant blows
down, the chemicals are lost along with the solid waste. If the cooling tower requires
additional blowdown, the water treatment may be insufficient.
This may be remedied by employing improved water treatment, which reduces the
formation of scale in a favorable way. You may also regulate the cooling system
programme to decrease the possibility of chemical blow down. Most of the time,
blowdowns happen in chillers as well.
2. High prices — The treatment of cooling towers using chemicals can be costly. This
covers both the initial planning expenditures and the ongoing maintenance costs. It
also covers the installation costs. The expense also covers the upkeep of the cooling
tower system's standard makeup and registry.
The facility must additionally pay a system discharge fee. The use of chemicals in the
plant raises the cost significantly. If you utilize non-chemical treatments, you can
save money as well. Choose from a variety of non-chemical cooling tower and chiller
treatments based on your budget.
3. Health hazards — Maintaining a cooling tower is difficult. The use of chemicals can
potentially expose anyone working on the tower to health dangers. The usage of
chemicals can lead to a variety of respiratory and breathing issues. Contaminated
water and chemicals can also cause respiratory difficulties. Most persons who work
near the tower are at danger of contracting Pontiac fever.
To reduce health problems, it is advisable to avoid the use of chemicals in cooling
towers and chillers. Natural therapy will ensure that such a health risk does not exist.
This will not only make the working environment safer, but also more secure. Natural
methods will not pose any health risks.
4. Water wastage (Bleed off) — The water that circulates around the tower has four
times the concentration required to operate the water cycle. The regular procedure of
eliminating one portion of concentrated water and replacing it with normal water is
known as bleed off. Most of the time, chemical-based water will leak out.
In a typical year, a cooling tower can bleed out up to one million gallons of water.
Other issues arise as a result of water waste. Fortunately, there are conservation
techniques that may significantly reduce bleed off. You can achieve this goal by using
a cooling water saving strategy.
Initiatives to Reduce Chemical Use and Implement Eco-Friendly Measures
It is critical to calculate and comprehend water concentration cycles. It is critical to check the
conductivity ratio in blow down. Increasing the number of concentration cycles will assist.
Increasing the number of cycles from three to six will help minimize the amount of makeup
water in the cooling tower. The installation of a conductivity controller can also aid in the
regulation of typical blowdown.
The installation of flow meters might assist you in determining the usual blowdown ratio.
Consider employing chemical-free treatments for both chillers and cooling towers. Non-
chemical water treatment has the potential to save a significant amount of money.
The Cooling Tower Electrolysis Treatment
This non-chemical treatment saves up to 80% of the blowdown water. The wastewater can
also be utilized for other purposes. It cleans sand filters with excellent efficiency. It has an
automated self-cleaning feature that removes accumulated scale and dust.
It generates a balanced PH environment, which inhibits rusting. It has a minimal running
cost and is completely safe for the environment. It also has a bleed control function that can
be turned on or off. This improves operating efficiency while simultaneously reducing energy
expenditures and discharge fees. Non-Chemical Water Treatment for Cooling Tower is
safe and cost-effective.
OUR TOP PRODUCTS:
Adiabatic Cooling System | Electrolytic Scale Remover | Automatic Tube Cleaning System | Vacuum Degasser system | Air & Dirt Separator |
Anti Fouling Condenser System | Closed Expansion Tank | Hydronic Systems